- 2018-02-05
- 特集 構造物とりこわし・解体工法 | 積算資料公表価格版
はじめに
建設分野においては周辺環境問題に対する意識が広く浸透し,新技術,新工法の開発・活用が多く行われている。解体・リニューアル工事等においても重機解体と併用して,低振動・低騒音の工法が選択されており,また特殊な条件下においてはアブレッシブウォータージェット工法による切断が行われている。
本稿では,コンクリートカッティング工法としてダイヤモンド工法,アブレッシブウォータージェット工法を紹介し,それぞれの課題をとりあげて改良を施した乾式ダイヤモンド工法,超高圧アブレッシブウォータージェット切断工法およびウォータージェット作業時の騒音の発生状況について紹介する。
1. 従来のダイヤモンド工法
人工ダイヤモンドを使用したダイヤモンド工具を用いて切断・穿孔する工法であり,重機等を使用した解体工法に対して,低振動・低騒音の工法として広く活用されてきている。
1-1 フラットソーイング工法
一般に床・床版・舗装のような水平面を切断する際に使用されている工法である。ダイヤモンドブレードを機械に取り付け,オペレータは機械の進行につれて歩きながら後方から一人で操作する。目地切,傷んだ舗装の打替・撤去のためのコンクリート部分の切断,電気・電話・ガス・水道・下水など舗装下に管を敷設する際の舗装部分の切断などに用いられている(写真- 1)。
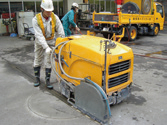
写真-1 フラットソーイング工法
1-2 コアドリリング工法
先端部に刃先をもった筒状の工具を回転させながら,その軸方向に圧力を加え,被穿孔物に工具を貫入させ,孔を開ける工法である。正確な円形切断を求められる現場で使用され,給排水管・電気配線・エアコンのダクトなど,どのような径の孔でも容易に穿孔できる。用途としては,主にケーブルやアンカーボルトを通したり,柱用の穴を開けたり,検査用のサンプルを採取したりする時に多く使用される(写真- 2)。
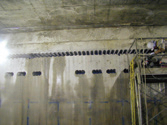
写真-2 コアドリリング工法
1-3 ウォールソーイング工法
切断面(壁面,斜面,床面等)にソーイングマシン走行用ガイドレールをアンカーボルトで固定し,そのレールにダイヤモンドブレードがセットされたソーイングマシンを装着して,ダイヤモンドブレードの高速な回転と,ソーイングマシンのレール上の移動によって,対象物を切断する工法である。用途としては,ビル,高速道路,地下鉄など,活用の場も広範囲に適用できる(写真- 3)。
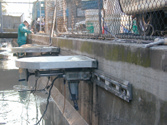
写真-3 ウォールソーイング工法
1-4 ワイヤーソーイング工法
ワイヤーソーを被切断物に巻き付けてループ状に両端を接続し,ガイドプーリーを用いて切断方向を調整し,ワイヤーソーに一定の張力を加えながら,駆動機により高速回転させて対象物を切断する工法である。被切断物の形状をほとんど選ばず自由に切断でき,柱や煙突のような大断面を一度に切断すること,病院や学校のような建物を一度に切断することも可能である(写真- 4)。
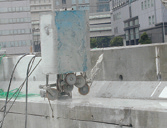
写真-4 ワイヤーソーイング工法
これら従来のダイヤモンド工法は切削時に冷却水を使用するため,排水汚泥が周辺環境に与える問題が指摘されている。この排水処理の問題に対応すべく,新たに開発された乾式ダイヤモンド工法について,次に紹介する。
2. 乾式ダイヤモンド工法
従来のダイヤモンド工法の機械を使用して,冷却水を無水もしくはほとんど使用せずに切断・穿孔をする工法である。主な特徴として以下のものが挙げられる。
①排水汚泥を少量にすることができ,周辺環境(河川等)への負荷を軽減できる。
②給排水設備が不要になる。
③産廃量が少なくなる。
①に関しては,河川や高速道路等に架かる橋や既存の建物を切断撤去する際に,周辺へ排水汚泥が漏水するリスクを軽減できる。また,寒冷地では冷却水が凍結し,作業員が足場上の作業で転倒・転落する災害を防ぐことができる。
②に関しては,従来ダイヤモンド工法では冷却水を供給するための給水設備が必要になり,水道等が敷設されていない現場では別途設備費用を計上する必要があった。また,切断により発生した排水汚泥は回収し適正な水処理を行うか,建設汚泥として産業廃棄処分をする必要があった。乾式ダイヤモンド工法は,冷却水をほとんど使用しないため,排水汚泥は集塵機等で回収することができ,上述のような大掛かりな設備は不要となる。
③に関しては,②でも述べた通り,切断により発生する廃材は切削粉として回収できるので,水分を含んだ排水汚泥よりも大幅に産廃量を軽減でき,そのままで産業廃棄処分が可能になる。以下に工種毎の特徴を記す。
2-1 乾式フラットソーイング工法
低水量タイプと冷却水を一切使用しない無水タイプの2種類がある。
低水量タイプのフラットソーは,専用の低水量ダイヤモンドブレードを使用し切断する。この際使用する機械は従来のフラットソーマシンと同様のものであり,冷却水の供給量を少量に設定して稼動させる。これにより排水汚泥は粘土状の塊として回収でき,従来切断時に必要なバキューム装置を使用せずに,簡易的に回収することが可能になった。床版撤去等の場合に,床版下部への排水汚泥の流出も軽減できる。切断深さは一般的に300mm程度まで可能である。
無水タイプのフラットソーは,フラットソーマシンに集塵機を搭載した機械(写真- 5)を使用する。
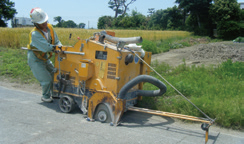
写真-5 乾式フラットソーイング工法
主に,建物等の目地切断で使用することが多い。切削粉はそのまま土嚢袋に回収できる。現在フラットソーにより舗装等を切断し発生した排水汚泥を,そのまま側溝等に排水できない条例を設けている自治体が増えてきている。ここで紹介する無水タイプのフラットソーは,アスファルト切断であれば一般的に100mm程度までは切断できる。ここ数年で,埼玉県内にて無水タイプのフラットソーで切断した実績も増えてきており,排水汚泥処理の問題に対処できる工法として期待できる。
2-2 乾式コアドリリング工法
従来のコアマシンに新式専用ビットを使用して穿孔する工法である。ビット内部にエアーを送りながら冷却し,ビットとマシンの接続部に専用の回収装置を取り付け集塵機で切削粉を回収する(写真- 6)。一般的にφ 150mmで500mm程度までの穿孔が可能である。
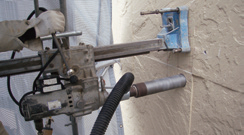
写真-6 乾式コアドリリング工法
2-3 乾式ウォールソーイング工法
従来のウォールソーマシンに乾式専用ブレードを使用して切断する工法である。冷却は乾式専用ブレードに少量の水をミスト状に噴霧し,直接ブレード基盤とダイヤモンドチップを冷却する。切断により発生した切削粉は,ウォールソーマシンのカバーに集塵機のホースを直接取り付け回収する方法であり,下向き施工で80%,横向き施工で60〜70%程度の回収が可能である。切断深さは一般的に200mm程度までである(写真- 7)。
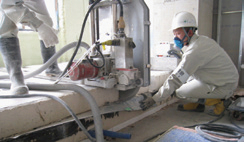
写真-7 乾式ウォールソーイング工法
2-4 乾式ワイヤーソーイング工法
従来のワイヤーソーマシンに乾式専用ワイヤーを使用して切断する工法である。切断ラインに合わせて防塵を兼ねたワイヤーカバーを設置し,切断中はサイクロン式の集塵機により切削粉を回収する(写真- 8)。
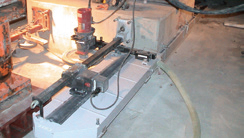
写真-8 乾式ワイヤーソーイング工法
乾式ワイヤーソーイング工法は平成20年5月に国土交通省NETIS(登録番号KT-080004-V)に登録されており,国内でも採用実績がある工法である。
3. 超高圧アブレッシブウォータージェット切断工法
超高圧水(圧力200〜300MPa程度)の噴流に研磨材(アブレッシブ材)を吸引混入させ,この水と研磨材の混合噴流をノズル先端より放出する。圧力200MPa時の流速は600m/sec以上に達する高速水噴流となり,この高速噴流エネルギーと研磨材がもつ切削性を利用し,様々な対象物に噴射して切断する工法である(写真- 9)。
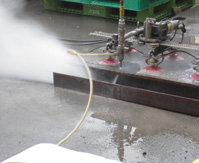
写真-9 超高圧アブレッシブウォータージェット工法
研磨材として最も多く利用されるガーネット(ざくろ石)はダイヤモンドに次ぐ硬度をもち,比重が4前後と重く破壊されにくいため,埃が立ちにくく浮遊シリカによる珪肺の心配もない,環境と人にやさしい天然の研磨材である。特別な場合には銅スラグ,スチールグリッドが利用される。
これらの研磨材を使用しない場合,単にウォータージェット工法と称され,コンクリート表面のはつりや各種コーティングの剥離などに用いられる。ウォータージェットは硬質な粗骨材や鉄筋を切断することができない。モルタル部分を破壊し粗骨材を堀り出しながら分離し切断を進めるため,鉄筋とコンクリートを同時に切断する用途には適さず,研磨材を用いるアブレッシブウォータージェットが用いられる。
[長所]
● ガス切断やプラズマアーク切断のような熱変形,熱変性が生じない。
● 大気への粉塵の発生がなく,刃物や加工物の振動による騒音が少ない。
● 非接触加工であるため,任意の位置で任意の形状に切断できる。
● あらゆる金属材料,コンクリートを切断でき,鉄筋コンクリート等の複合材料も切断できる。
● ノズルは小型,軽量であり自動化,ロボット化が可能であり遠隔制御も容易である。
[短所]
● 噴射音が大きく,カバー等による騒音対策が必要である。
● 噴射水,使用済研磨材の処理が必要である。
● 安全面により,ノズルはロボットやガイドレール等で保持することが必要である。
● 一般の解体工事で使用するには切断能力が小さい。
アブレッシブウォータージェットの加工効率を向上させるには,噴射する研磨材の高速化によって運動エネルギーを高める必要があり,研磨材の高速化には水噴流の高速化が必要不可欠である。ウォータージェットの噴射速度は圧力の平方根に比例するため,同一動力におけるアブレッシブウォータージェットでは,低圧大流量よりも高圧小流量のほうが加工効率は向上する。
研磨材,排水に関わる費用(研磨材購入費用,消耗部品費用,処理費用など)はアブレッシブウォータージェットにおけるランニングコストの大半を占めることが多く,同一圧力で研磨材使用量(単位時間当り)を増加すると切断速度の向上が図れるが,研磨材消費量(単位加工長さ当り)が増加する。同一の研磨材使用量(単位時間当り)で高圧化を図ると切断速度の向上だけでなく,研磨材消費量(単位加工長さ当り)を低減できることが多い。経済的で効率的なアブレッシブウォータージェット切断工法を目指すうえで高圧化は欠かすことができないアプローチとなっている。
分野は異なるが航空機業界や自動車業界等における各種部品加工に用いられるアブレッシブウォータージェットでは圧力が最高で600MPaにも達するシステムが採用されるなど,切断性能と経済性を向上させた事例が出てきている。これらの業界とは異なり,建設分野で用いられるウォータージェットは超高圧水の伝送に超高圧ホースが用いられるのが普通であり,超高圧ホースが持つ耐圧の範囲内の圧力で施工される。今後の技術革新により,周辺機器を含めたシステム全体の高圧化に向けた開発やシステムの効率化が進むことにより,これまで以上にアブレッシブウォータージェットが利用されるものと考える。
アブレッシブウォータージェット工法の基本機能を図-1に,超高圧アブレッシブウォータージェット装置の全体仕組み(システム)を図-2に示す。
(以上,第一カッター興業株式会社 砂川 高寛)
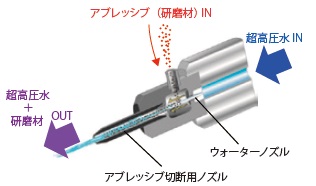
図-1 アブレッシブウォータージェット工法の基本機能図
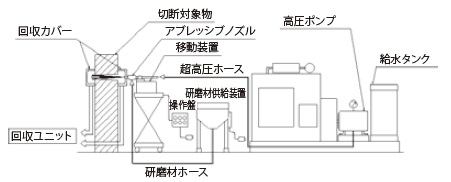
図-2 超高圧アブレッシブウォータージェット装置の全体仕組み(システム)図
4. 超高圧ウォータージェットを用いた削孔装置
コンクリート構造物の耐震補強や不要部分の撤去に対して,超高圧水を用いた削孔方法が用いられている。ここでは下向き削孔装置と水平削孔装置について紹介する。
(1)下向き削孔装置
耐震補強のためにアンカー筋を増やす工事の際に使用される削孔装置について説明する。削孔を行う回転軸は1.5〜2mのランスとなっており,先端部に2穴のノズルヘッドを取り付けて回転させながら超高圧水を送り込んで削孔していくものである。
装置全景を写真- 10に示す。ウォータージェット(以下,WJ)能力は200MPa× 23リットル/分を使用。削孔後の状況は写真- 11に示すように約φ50mmの削孔となった。
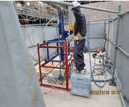
写真-10 装置全景
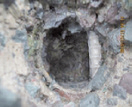
写真-11 削孔後の状況
写真- 12には下向き削孔の施工状況を示す。
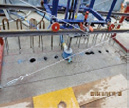
写真-12 下向き削孔の施工状況
複数本の削孔には現場合わせでガイドレールを取り付け装置の横移動ができるように工夫した。削孔径φ 50〜60mm,深さ約500mm程度で1本当り20〜30分の施工時間であった。削孔能力は現場ごとに据え付け架台や装置治具を作成するためまちまちとなる。削孔深さに対しては500mmを超えるごとに回転軸を継ぎ足して実施する。
写真の先端部のお椀状の機器はバキューム装置で,掘削時に発生する掘削ずりや排水を吸引撤去する。
(2)水平削孔装置
壁などの構造体の補強工事などに使用するものであり,写真- 13に水平削孔装置全景を示す。
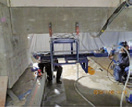
写真-13 水平削孔装置全景
掘削部は下向き掘削と同タイプの回転軸を使用する。装置支持架台は下向き削孔の場合と同様,現場条件に合わせて製作・設置する。写真- 14 に施工状況を示す。
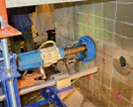
写真-14 施工状況
WJ能力は下向き削孔と同様の200MPa×23リットル/分を採用した。削孔能力は削孔径約φ60mm,1m深さで40〜50分であった。これ以上の削孔には回転軸を継ぎ足して実施する。
写真- 15には削孔径の状態を,写真- 16にはバキューム回収装置類を示す。
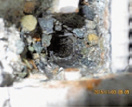
写真-15 削孔径の状態
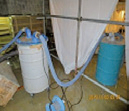
写真-16 バキューム回収装置類
下向きと水平での能力差は,下向きの際,削孔底に掘削片が溜りその除去に時間がかかること,それぞれの対象コンクリート仕様や条件の違いなどが原因と考えられる。
WJ による削孔が採用された理由は,
● 打撃装置や機械的切削装置が直接構造物を打撃・破砕接触していくのと違い,ノズルから噴射した超高圧水のエネルギーによりコンクリートを除去していくので母材を余分に傷めないこと
● 万一,鉄筋と接触しても損傷を与えないことなどの特長が評価されたためと言える。
(以上,株式会社アシレ 森 謙一)
5. コンクリート構造物の高電圧放電破砕工法
近年,都市化に伴い,騒音・振動が大きな発破工法は使用できず,大型掘削(切削)機械や割岩工法は掘削能力に限界があり,工事が難渋することが多い。高電圧放電破砕工法は,このような背景から開発された岩盤破砕技術である。
本工法には,水と電気だけで岩を割るギャップ方式と補助薬入りのカートリッジを使用する線爆方式がある。岩が割れればコンクリートも割れることから構造物の解体事例が増えている(図- 3)。

図-3 岩の破壊機構の違いによる分類
5-1 工法概要
本技術は電源から充電器を介してコンデンサに蓄積した電気エネルギーを対象物の穿孔内に挿入した電極棒の先端から一気に放電させ,その時に発生する衝撃波(プラズマ)で岩やコンクリート構造物を破砕する(図- 4)。
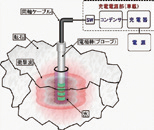
図-4 システム概要(ギャップ方式)
ギャップ方式は,電気エネルギーのみを利用して非圧縮体の水を衝撃波の伝播に使用する。線爆方式では細線の溶融気化により補助薬の燃焼時に発生するガス圧を利用している。これまでの発破技術と異なり騒音,振動が少なく,破砕力は,放電圧の大きさや補助薬の量で調整できるため,構造物の近傍でも施工できることが特長である。
5-2 電磁誘導・漏洩電流および振動・騒音測定
本工法の普及展開にあたり,高電圧放電により発生するプラズマが周辺電気機器に及ぼす影響を調査するため,「漏洩電流測定」,「電磁測定誘導」とプラズマ破砕による振動・騒音を測定した。写真- 17 に測定状況を示す。
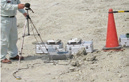
写真-17 振動・騒音測定状況
(1)電磁誘導および漏洩電流測定結果
電磁誘導,漏洩電流ともに検知されなかった。
(2)騒音・振動測定結果(表- 1)
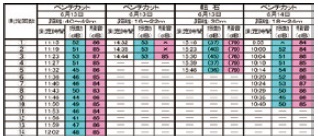
表-1 振動・騒音測定結果
プラズマ破砕による振動・騒音を16〜49mの距離で測定した結果,最大値は振動レベルで54dB,騒音レベルでは87dBが計測された。これら最大値を「気象庁震度階級別振動レベル換算表」「騒音の例(公害防止の技術と法規 騒音編)」に当てはめると,次の範囲に該当する。
①振動レベル:54dB →「震度0,無感」,「人は揺れを感じない」
②騒音レベル:87dB →「地下鉄電車内,バス車内」であるが,これら測定値は,常時発生している振動・騒音ではなく,2/10,000秒の放電に伴う瞬時に発生するもので,実際は周辺環境に及ぼす影響は少なかった。
写真- 18は橋脚の解体事例で,放電破砕後の二次破砕にブレーカではなくバックホーを採用した事例である。
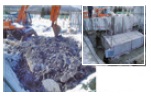
写真-18 橋脚の解体前と解体時
あとがき
構造物を壊す動力源は,《空圧》から《油圧》へと推移して装置も大型化し,その躍進は目覚ましい。近年,この破砕に電気エネルギーを適用しようとする動きがあり,次世代のクリーンな破壊エネルギーとして期待できる。
(以上,株式会社ファテック 垣内 幸雄)
第一カッター興業株式会社砂川 高寛 株式会社ファテック 垣内 幸雄
【出典】
積算資料公表価格版2017年11月号
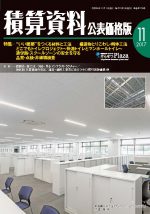
- 構造物とりこわし工【ロックラック】|カヤク・ジャパン(株)
- 構造物とりこわし工【NRC】|NRCジャパン(株)
- 構造物とりこわし工【スーパーウェッジ/ロックバスター】|(株)クキタ
- 構造物とりこわし工【ミニブラスティング工法】|(株)カコー
- 構造物とりこわし工【スーパービッガー工法】|(株)カコー
- 構造物とりこわし工【乾式ワイヤーソーイング工法】|第一カッター興業(株)
- 構造物とりこわし工【コリジョンジェット工法】|(株)ケミカル工事
- 構造物とりこわし工【ガンサイザー】|日本工機(株)
- 構造物とりこわし工【ヒロワーク Kmighty工法】|地中埋没物撤去技術協会
- 構造物とりこわし工【ミニブラスティング工法】|(株)相模工業
最終更新日:2023-07-10
同じカテゴリの新着記事
- 2025-06-19
- 建設現場における熱中症対策 | 積算資料公表価格版
- 2025-06-19
- 特集 雪寒対策資機材 | 積算資料公表価格版
- 2025-06-19
- 特集 雪寒対策資機材 | 積算資料公表価格版
- 2025-06-19
- 特集 雪寒対策資機材 | 積算資料公表価格版